FAQ: Advancements in SLA/DLP Resin Technology
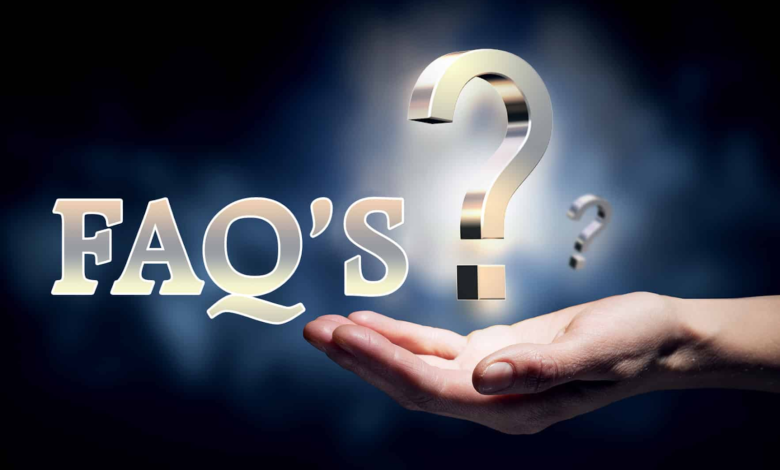
1. General Information on SLA/DLP Additive Manufacturing
Q1: What are SLA and DLP technologies?
A: Stereolithography (SLA) and Digital Light Processing (DLP) are resin-based additive manufacturing (AM) technologies that use photopolymerization to create high-precision parts with excellent mechanical properties.
Q2: How do SLA and DLP compare to other 3D printing methods?
A: SLA/DLP provide higher resolution, isotropic mechanical properties, smoother surface finishes, and faster material changeover compared to Fused Deposition Modeling (FDM) and Selective Laser Sintering (SLS).
Q3: What are the advantages of SLA/DLP printing?
A: Key advantages include high resolution (as fine as 25 µm), superior surface quality, rapid material swapping, fast print speeds (especially with DLP), and a diverse selection of high-performance resins 3d printing.
Q4: What limitations have historically affected SLA/DLP resins?
A: Older resin formulations were brittle and degraded over time. However, modern high-performance resins now rival traditional thermoplastics in toughness, impact resistance, and temperature stability.
2. SLA/DLP Resin Advancements
Q5: How have SLA/DLP resins improved over time?
A: New resin formulations feature enhanced toughness, high-temperature resistance, ceramic fillers for wear resistance, and biocompatibility. Some resins also support multi-cure processes for improved mechanical properties.
Q6: What are hybrid multi-cure systems?
A: These resins incorporate dual or multi-cure chemistries, allowing for secondary thermal curing to enhance strength, impact resistance, and heat tolerance.
Q7: What types of resins are available for SLA/DLP printing?
A: SLA/DLP resins include thermoplastic analogs, flexible elastomers, high-temperature materials, biocompatible photopolymers, and ceramic-filled composites.
3. Applications of SLA/DLP Printing
Q8: What industries benefit from SLA/DLP printing?
A: SLA/DLP is used in aerospace, automotive, medical, dental, and industrial manufacturing due to its precision, material versatility, and scalability.
Q9: How is SLA/DLP used in aerospace and automotive applications?
A: SLA/DLP enables the production of flame-retardant and high-temperature-resistant parts that meet aerospace and automotive regulatory standards.
Q10: Are SLA/DLP materials suitable for medical applications?
A: Yes, biocompatible resins certified under ISO 10993-5 and -10 support surgical guides, prosthetic components, and soft-tissue simulation models.
Q11: How does SLA/DLP support industrial manufacturing?
A: Wear-resistant ceramic resins enable the production of mold masters, jigs, fixtures, and even short-run injection molds.
4. SLA/DLP vs. Other Manufacturing Methods
Q12: How does SLA/DLP compare to injection molding?
A: SLA/DLP provides cost-effective, high-quality parts for low- to mid-volume production, with greater design flexibility and faster turnaround than injection molding.
Q13: How does SLA/DLP reduce production costs?
A: SLA/DLP minimizes material waste, requires less post-processing, and supports faster print speeds compared to powder-bed fusion and filament-based AM systems.
Q14: Can SLA/DLP printers swap materials easily?
A: Yes, unlike powder-based or filament-based systems, SLA/DLP resins can be swapped in minutes, enabling flexible multi-material workflows.
5. Future of SLA/DLP in Manufacturing
Q15: Is SLA/DLP a viable alternative to traditional manufacturing?
A: Yes, with advancements in resin formulations, SLA/DLP has evolved beyond prototyping into full-scale production, offering a viable alternative to traditional thermoplastics and injection molding.
For more information, visit RapidMade.
This FAQ condenses key insights from the white paper into a clear and structured format. Would you like any modifications or additional questions?
You said:
Can you get it to 25 questions?
ChatGPT said:
Certainly! Below is an expanded FAQ with 25 questions:
FAQ: The Material Versatility of SLA/DLP Resins in Additive Manufacturing
1. General Information on SLA/DLP Additive Manufacturing
Q1: What are SLA and DLP technologies?
A: Stereolithography (SLA) and Digital Light Processing (DLP) are resin-based additive manufacturing (AM) technologies that use photopolymerization to create high-precision parts with excellent mechanical properties.
Q2: How do SLA and DLP differ from each other?
A: SLA uses a laser to cure liquid resin point by point, while DLP cures entire layers at once using a digital light projector, making it faster for certain applications.
Q3: How do SLA and DLP compare to other 3D printing methods?
A: SLA/DLP provides higher resolution, isotropic mechanical properties, smoother surface finishes, and faster material changeover compared to Fused Deposition Modeling (FDM) and Selective Laser Sintering (SLS).
Q4: What are the key advantages of SLA/DLP printing?
A: High resolution (as fine as 25 µm), superior surface quality, rapid material swapping, fast print speeds (especially with DLP), and a diverse selection of high-performance resins.
Q5: What limitations have historically affected SLA/DLP resins?
A: Older resin formulations were brittle and degraded over time. However, modern high-performance resins now rival traditional thermoplastics in toughness, impact resistance, and temperature stability.
2. SLA/DLP Resin Advancements
Q6: How have SLA/DLP resins improved over time?
A: New resin formulations feature enhanced toughness, high-temperature resistance, ceramic fillers for wear resistance, and biocompatibility. Some resins also support multi-cure processes for improved mechanical properties.
Q7: What are hybrid multi-cure systems?
A: These resins incorporate dual or multi-cure chemistries, allowing for secondary thermal curing to enhance strength, impact resistance, and heat tolerance.
Q8: What are nanocomposite and ceramic-filled resins?
A: These resins contain nano-sized ceramic or glass fillers, providing enhanced wear resistance, dimensional stability, and high-temperature performance.
Q9: What types of resins are available for SLA/DLP printing?
A: SLA/DLP resins include thermoplastic analogs, flexible elastomers, high-temperature materials, biocompatible photopolymers, and ceramic-filled composites.
Q10: Can SLA/DLP resins simulate injection-molded plastics?
A: Yes, advanced resins can replicate the mechanical and thermal properties of traditional thermoplastics like ABS, polypropylene (PP), and ULTEM.
3. Applications of SLA/DLP Printing
Q11: What industries benefit from SLA/DLP printing?
A: SLA/DLP is used in aerospace, automotive, medical, dental, and industrial manufacturing due to its precision, material versatility, and scalability.
Q12: How is SLA/DLP used in aerospace and automotive applications?
A: SLA/DLP enables the production of flame-retardant and high-temperature-resistant parts that meet aerospace and automotive regulatory standards.
Q13: Are SLA/DLP materials suitable for medical applications?
A: Yes, biocompatible resins certified under ISO 10993-5 and -10 support surgical guides, prosthetic components, and soft-tissue simulation models.
Q14: How does SLA/DLP support industrial manufacturing?
A: Wear-resistant ceramic resins enable the production of mold masters, jigs, fixtures, and even short-run injection molds.
Q15: Can SLA/DLP be used for dental applications?
A: Yes, specialized biocompatible resins allow for the production of crowns, bridges, dentures, and surgical guides with exceptional precision.
4. SLA/DLP vs. Other Manufacturing Methods
Q16: How does SLA/DLP compare to injection molding?
A: SLA/DLP provides cost-effective, high-quality parts for low- to mid-volume production, with greater design flexibility and faster turnaround than injection molding.
Q17: How does SLA/DLP reduce production costs?
A: SLA/DLP minimizes material waste, requires less post-processing, and supports faster print speeds compared to powder-bed fusion and filament-based AM systems.
Q18: Can SLA/DLP replace powder-bed fusion (PBF) methods like SLS?
A: While SLS is preferred for large-scale polymer part production, SLA/DLP offers better surface quality, faster post-processing, and easier material handling.
Q19: How does SLA/DLP differ from FDM?
A: SLA/DLP produces parts with higher resolution, better mechanical isotropy, and superior surface finish compared to FDM, which has visible layer lines and weaker interlayer bonding.
Q20: How do material changeover times compare across AM technologies?
A: SLA/DLP allows for material swaps in minutes, whereas powder-based and filament-based systems require extensive purging, sieving, or cleaning.
5. Future of SLA/DLP in Manufacturing
Q21: Is SLA/DLP a viable alternative to traditional manufacturing?
A: Yes, with advancements in resin formulations, SLA/DLP has evolved beyond prototyping into full-scale production, offering a viable alternative to traditional thermoplastics and injection molding.
Q22: What role does SLA/DLP play in Industry 4.0?
A: SLA/DLP supports agile, on-demand manufacturing with digital workflows, enabling businesses to produce customized parts quickly and efficiently.
Q23: Can SLA/DLP print multi-material parts?
A: While SLA/DLP is primarily single-material, some hybrid workflows enable multi-material printing by swapping resins mid-process or post-processing composite structures.
Q24: What are the environmental impacts of SLA/DLP printing?
A: SLA/DLP reduces material waste compared to traditional manufacturing, but photopolymer resins require proper disposal and handling due to their chemical composition.
Q25: How will SLA/DLP technology evolve in the future?
A: Future developments will focus on expanding resin performance, improving sustainability, and integrating SLA/DLP into automated manufacturing systems for high-volume production.
For more information, visit RapidMade.