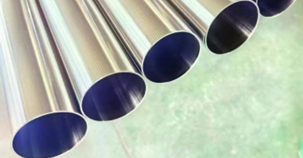
Aerospace engineering demands materials that can withstand some of the most extreme conditions on earth and beyond. These materials must endure high temperatures, intense pressures, and corrosive environments, all while maintaining structural integrity and strength. Among the various metals used in the aerospace industry, Monel metal stands out as a critical alloy due to its unique combination of properties.
Monel metal is well-known for its exceptional corrosion resistance, high strength, and ability to maintain stability under extreme conditions. Monel suppliers play a key role in providing this crucial material to industries that require high-performance alloys.
What Is Monel Metal?
Monel metal is a group of nickel alloys, with the most common grades being Monel 400 and Monel K-500. These alloys typically consist of 52-67% nickel, along with copper, iron, and trace amounts of manganese and other elements. The exact composition depends on the grade, with Monel K-500 containing small additions of aluminum and titanium for increased strength and hardness.
Monel 400: This is the most widely used Monel alloy and is known for its excellent corrosion resistance, especially in seawater and acidic environments. It also offers good mechanical properties and maintains strength over a wide range of temperatures.
Monel K-500: This alloy is similar to Monel 400 but has increased strength and hardness due to the addition of aluminum and titanium. It is often used in aerospace applications that require materials with high fatigue strength.
Why Monel Metal Is Ideal for Aerospace Applications
Monel metal’s properties make it highly suitable for use in aerospace engineering. The key characteristics that stand out are its corrosion resistance, high-temperature stability, and strength under stress. These properties enable Monel metal to handle extreme conditions that are commonly encountered in aerospace environments.
1. High-Temperature Resistance
Aerospace components are often exposed to extreme heat, particularly in engines and exhaust systems. Materials used in these applications must maintain their mechanical properties even at elevated temperatures.
Monel metal can withstand temperatures up to 1000°F (538°C) without losing its strength or becoming brittle. This makes it an ideal material for use in turbine blades, combustion chambers, and exhaust manifolds where high temperatures are prevalent.
For example, Monel K-500 has been used in gas turbine engines due to its ability to resist heat and retain its mechanical properties over prolonged periods of operation. The alloy’s resistance to heat-induced deformation ensures that components remain reliable and functional, even in the most demanding conditions.
2. Corrosion Resistance
Corrosion is a major concern in the aerospace industry, particularly for components exposed to harsh environments such as saltwater, fuel, and other chemicals. Monel metal offers excellent corrosion resistance, particularly in marine and acidic environments.
Monel 400, for example, provides exceptional resistance to seawater, making it a preferred material for aerospace components used in coastal or marine environments. This corrosion resistance also extends to acidic solutions, such as sulfuric and hydrofluoric acids, which are encountered in certain aerospace applications.
Additionally, Monel metal’s resistance to corrosion makes it a reliable choice for components exposed to the fuels and lubricants used in aircraft engines. Its ability to resist both oxidation and corrosion allows for a longer lifespan of components, reducing maintenance needs and costs.
3. Strength and Durability Under Stress
Aerospace components are subject to high stress, particularly in areas like landing gear, fasteners, and structural supports. These parts must be able to withstand repeated loading and unloading without experiencing fatigue or failure.
Monel K-500 offers superior tensile strength and fatigue resistance, making it well-suited for aerospace components that endure high mechanical loads. This grade of Monel metal maintains its strength even after long periods of cyclic loading, which is crucial for ensuring the structural integrity of critical aerospace components.
The alloy’s ability to resist fatigue also extends to environments where stress corrosion cracking is a concern. Monel metal’s superior fatigue resistance ensures that it can handle repeated mechanical stress without cracking, which is essential for the safety and longevity of aerospace equipment.
Applications of Monel Metal in Aerospace
Due to its combination of properties, Monel metal is used in a variety of aerospace components. Here are some specific examples of how this metal is applied within the industry.
1. Fuel Tanks and Fuel Lines
Monel metal’s resistance to both corrosion and stress cracking makes it an excellent material for fuel tanks and fuel lines. These components must remain impervious to the chemicals in jet fuels, as well as any environmental factors that may contribute to corrosion.
Monel 400 is frequently used for fuel storage and transfer systems because of its ability to resist the corrosive effects of fuels, oils, and other liquids commonly used in aircraft. Its corrosion resistance ensures that fuel tanks and lines remain leak-free and operational for extended periods.
2. Exhaust Systems and Heat Exchangers
Exhaust systems in aircraft are subjected to extremely high temperatures and corrosive gases. Monel metal’s heat and corrosion resistance make it an ideal material for these components.
Monel K-500 is commonly used in exhaust systems and heat exchangers due to its ability to handle extreme temperatures and corrosive exhaust gases without degrading. Its stability at high temperatures ensures that these components remain effective, reducing the risk of failure.
3. Fasteners and Bolts
In aerospace, the reliability of fasteners is critical. Monel metal is frequently used for fasteners in areas exposed to extreme environmental conditions, such as marine and offshore aerospace applications.
Monel K-500 is often used to manufacture bolts, screws, and fasteners because of its strength and resistance to corrosion. These fasteners are particularly beneficial in aerospace environments where they may be exposed to saltwater, extreme temperatures, or chemical exposure.
4. Landing Gear Components
Landing gear components must endure significant mechanical stress during takeoff, landing, and taxiing. Monel metal’s fatigue resistance makes it ideal for these high-stress components.
Monel K-500 is used in various landing gear components because it can handle repeated impact and stress without succumbing to fatigue. Its high strength-to-weight ratio also makes it valuable in reducing the overall weight of the aircraft without compromising structural integrity.
Challenges in Using Monel Metal
While Monel metal offers numerous advantages in aerospace applications, there are also some challenges to consider. The cost of Monel metal is higher than that of other alloys like stainless steel, primarily due to its nickel content. However, its longer lifespan and superior performance often justify the higher upfront costs.
Additionally, Monel metal can be difficult to machine due to its toughness. Specialized tools and techniques are required to machine and fabricate components from Monel metal without causing excessive wear on the equipment.
Conclusion
In the aerospace industry, reliability, durability, and safety are paramount. Monel metal offers a unique combination of properties that make it an ideal material for handling the extreme conditions commonly encountered in aerospace applications. Its resistance to high temperatures, corrosion, and mechanical stress ensures that components made from Monel metal remain reliable and functional in the most demanding environments.